Digital services for railways
Whether it’s superior reliability, guaranteed availability, or better lifecycle cost efficiency, our digital services are the key to achieving your business objectives. From connectivity and measurement technology to intelligent algorithms and precise analytics, we offer a comprehensive portfolio for optimized maintenance operations – supported by decades of practical experience.
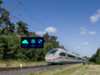
Whether it’s superior reliability, guaranteed availability, or better lifecycle cost efficiency, our digital services are the key to achieving your business objectives. From connectivity and measurement technology to intelligent algorithms and precise analytics, we offer a comprehensive portfolio for optimized maintenance operations – supported by decades of practical experience.