PROFINET in the manufacturing industry
From single machines to entire production plants: The PROFINET Industrial Ethernet standard is the basis for high product quality and reliability in the manufacturing industry. This is ensured by PROFINET particularly thanks to its fast, deterministic real-time communication as well as its integrated safety and diagnostic functions.
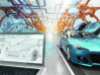
From single machines to entire production plants: The PROFINET Industrial Ethernet standard is the basis for high product quality and reliability in the manufacturing industry. This is ensured by PROFINET particularly thanks to its fast, deterministic real-time communication as well as its integrated safety and diagnostic functions.